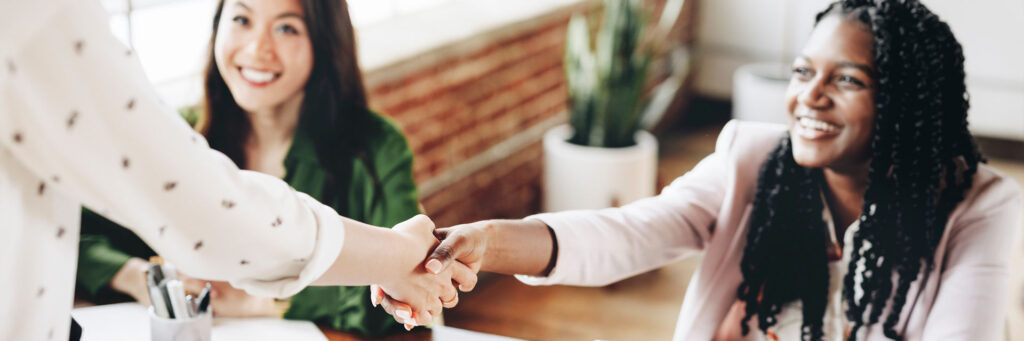
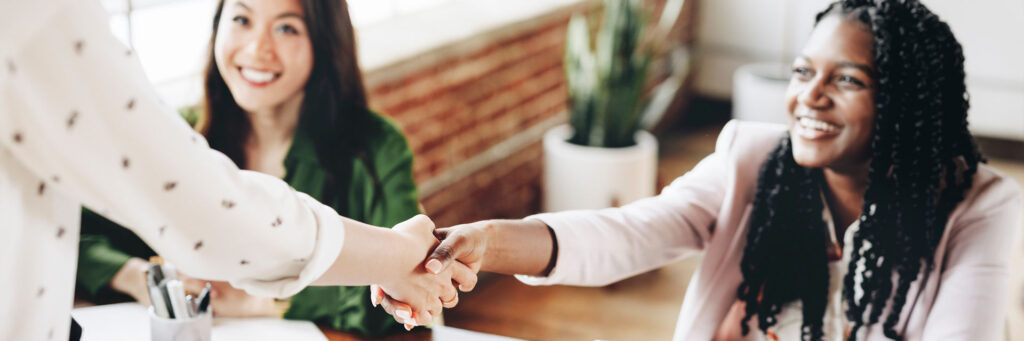
The WAGO Group, headquartered in Minden, electrical connection technology and automation for many decades . The company has now opened a new chapter in terms of transformation and sustainability: In September 2023, it brought a product onto the market for the first time that is partly made from recycled and bio-based residues .
Plastic is both a solution and a challenge. According to the company, the WAGO Group from Minden in Westphalia, for example, has developed into the world market leader in spring clamp technology . WAGO products used in all types of electrical installations The company now has around 60,000 different items , many of which are produced in millions. Most are quite small – like a sugar cube. And almost all of them consist of plastic . It is light, robust - and based on a fossil raw material , namely oil. This raw material is finite.
The extraction and processing of also pollutes environment . Furthermore, huge amounts of plastic do not end up in recycling, but in waste incineration plants . This also has negative consequences for the environment and the climate. More and more companies that produce plastic products are therefore working on alternatives . WAGO is one of them. The group's products and solutions are used in industry, railway and energy technology, marine and offshore, building and lighting technology. Worldwide .
“We draw a lot of innovative strength from this close regional network.”
As part of its sustainability strategy, the Minden-based group of companies has set itself the goal reducing the proportion of new plastic in its products . In September 2023, WAGO brought the first connecting clamp onto the market that contains plastic components made from recycled plastics and bio-based residues . According to the company, the series 221 connecting terminal is one of WAGO's best-known products; many companies around the world use it in electrical installations. Since September, they have been able to choose between the conventional product – recognizable by its orange levers – and the more ecological version with green levers. Residual materials from industry and households are used here. They are certified of origin and come from a circular process. Recycled plastics are also added, so-called post-consumer recyclate . As a result, the connecting clamp saves fossil resources and keeps plastics in the cycle. “The levers consist of at least 27 percent reused PET bottles ,” explains Astrid Burschel, Vice President Corporate Sustainability of the WAGO Group, “the basis of the housing is made up of up to 77 percent bio-based residues such as tall oil, used grease and residues from the production of Cooking oils.” Thanks to appropriate processes, these can now be processed into high-quality polycarbonate . also focusing on more sustainability packaging It consists of grass paper with a grass fiber content of up to 30 percent and a recycled paper content of around 70 percent .
The company was founded in 1951 , and Minden remains the headquarters. Of the 9,000 employees worldwide, around 3,000 work at their home location. WAGO is not only rooted in the location as a large employer, but also actively involved in overcoming current and future challenges together. WAGO is a partner of it's OWL , the technology network Intelligent Technical Systems OstWestfalenLippe, which also includes many research institutions. Numerous collaborations are being carried out here to develop solutions for digital and sustainable transformation in medium-sized businesses. innovative strength from this close regional network ,” emphasizes Burschel. The WAGO Group is also involved in the RailCampus OWL , in which manufacturers, universities, Deutsche Bahn and local authorities deal with the rail technology of the future. The group also recruits a lot of young talent in the region for training and dual studies.
This success story of an innovative transformation was published in January 2024. There will be no updates or checks of the information afterwards.
The publication series “Transformation through Innovation” is intended to illustrate how companies in North Rhine-Westphalia have been able to write successful innovation stories thanks to the framework conditions created by the state of North Rhine-Westphalia.
Are you interested in being featured in a future edition?
Then contact us with your request at: