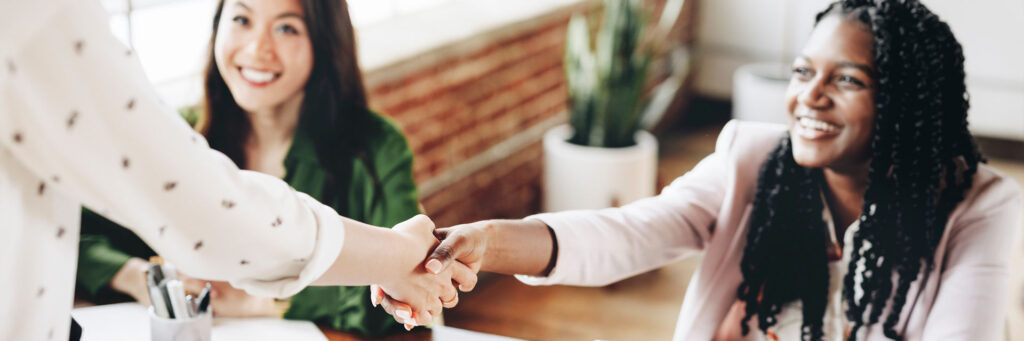
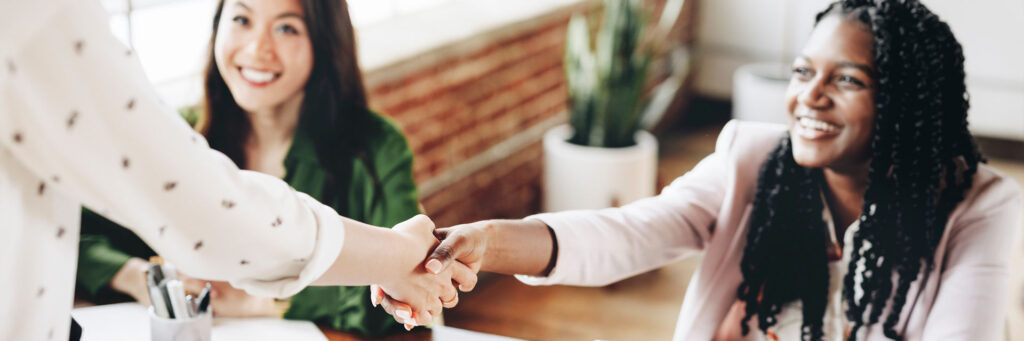
Oskar Lehmann GmbH & Co. KG from Blomberg-Donop near Lemgo specializes in technical plastic parts , for example for the furniture and automotive industries . recyclates and bio-based plastics is expected to continue to increase.
Plastic is the solution for numerous applications in business and everyday life. The material has important properties such as hardness and formability, elasticity and breaking strength, which can be varied to a large extent. But plastic also causes problems. The starting product for plastic are carbon compounds from crude oil or natural gas, i.e. from fossil raw materials. But it is not just the consumption of a finite resource that is problematic. In addition, processing is energy-intensive. And: Huge amounts of plastic are not recycled, but end up in landfills, in waste incineration plants and often directly in nature - with further negative consequences for the environment and climate. That's why alternatives have been researched for a long time.
The Oskar Lehmann company from East Westphalia, founded in 1961, began looking into the question of how products – such as cable glands, gliders and plugs, caps and covers – could be made more sustainable in 2006. The impetus came from a customer from the Netherlands, a dealer in office furniture accessories. He suggested switching to bio-based plastic, namely plastic based on potato starch. This couldn't be achieved in the long term, but the starting signal had been given.
“More and more companies are now taking sustainability seriously.”
Since then, the company has been working on bio-based plastics and products made from recycled materials. The biggest challenge: “Acceptance,” says managing director Melanie Lehmann. “Of course, each of our standard and special products must meet the desired material properties.” This is now often the case with alternatives to the petrochemical starting product or at least with bio-based admixtures. But it takes time until this is really accepted. The company has dealt intensively with the topic in projects with universities and has built up a lot of know-how.
In autumn 2023 the time has come: the first cable bushing will be brought onto the market that is not made of conventional plastic, but rather of the bioplastic “AgriPlast” from the manufacturer Biowert. It contains up to 75 percent quickly renewable natural fibers, namely cellulose from grass. Thermoplastics, such as recycled polypropylene, make up a significantly smaller proportion. “The cable feedthrough for office tables has all the desired properties – from appearance to flexibility to durability,” says Lehmann, “but it uses much less energy and resources during production and therefore protects the climate.” At the same time, you work at Oskar Lehmann is already working on other products based on bioplastics. “We have recently noticed that acceptance is increasing,” says the managing director happily, “more and more companies are now taking sustainability seriously.” At Oskar Lehmann, resource conservation also means that products are increasingly being designed in such a way that individual parts can be replaced. In addition, the company is constantly reducing the amount of waste in production. Unavoidable waste is collected and processed and flows into our own product range as recyclate.
In order to create alternatives to conventional plastic and to produce products based on this, a lot of research and development work is necessary. “We are therefore extremely happy with our location here in East Westphalia-Lippe,” reports Lehmann, with a view to the existing skills in the region. “There are many interesting partners here in the areas of plastics, the circular economy and digitalization.” Your company works to For example, we work closely with the Ostwestfalen-Lippe University of Technology and the Institute for Plastics Management OWL. There are also regular projects and topics that we work on together with Bielefeld University. The company is also a partner in the “Lippe circular” consortium, in which over 40 actors from business, society, research and municipalities are committed to sustainable and circular economy processes. “A lot is happening here,” says Lehmann, praising the location. In a project with a local daycare center, the company also taught young children interesting facts about plastic, recycling and sustainability.
This success story of an innovative transformation was published in October 2023. There will be no updates or checks of the information afterwards.
The publication series “Transformation through Innovation” is intended to illustrate how companies in North Rhine-Westphalia have been able to write successful innovation stories thanks to the framework conditions created by the state of North Rhine-Westphalia.
Are you interested in being featured in a future edition?
Then contact us with your request at: